Top 10 OSHA Safety Violations and How to Avoid Them
- Sam Spaccamonti
- Nov 21, 2024
- 4 min read
Occupational Safety and Health Administration (OSHA) regulations are critical for maintaining workplace safety. Each year, certain violations consistently appear on OSHA's list of the most frequently cited standards. Understanding these violations and how to prevent them is essential for employers and employees alike. This article will delve into the top 10 OSHA safety violations for 2024, provide examples of OSHA violations, and offer practical strategies to avoid them.
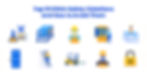
Top 10 OSHA Safety Violations: How to Stay Compliant
1. Fall Protection – General Requirements
Fall protection remains the most frequently cited violation, with 6,307 instances reported in 2024. Falls account for a significant number of workplace injuries and fatalities, particularly in construction settings.
How to Avoid:
Implement Guardrails: Install guardrails, safety nets, or personal fall arrest systems where employees work at heights.
Training: Provide comprehensive training on fall hazards and the use of protective equipment.
Regular Inspections: Conduct routine inspections of fall protection systems to ensure they are functioning correctly.
2. Hazard Communication
This standard addresses the communication of hazards associated with chemicals in the workplace. In 2024, 2,888 violations were noted.
How to Avoid:
Safety Data Sheets (SDS): Ensure that SDS are available for all hazardous substances and that employees know how to access them.
Training Programs: Implement training programs that educate employees on chemical hazards and proper handling procedures.
Labeling: Use clear and consistent labeling on all hazardous materials.
3. Ladders
In 2024, 2,573 citations were issued for ladder safety violations. Improper ladder use or maintenance can lead to serious injuries.
How to Avoid:
Regular Maintenance: Inspect ladders regularly for defects and remove any damaged ladders from service.
Proper Use Training: Train employees on safe ladder practices, including how to set up ladders correctly and maintain three points of contact.
Height Regulations: Ensure extension ladders extend at least three feet above the landing surface.
4. Respiratory Protection
Respiratory protection violations were cited 2,470 times in 2024. These violations often occur when employers fail to provide adequate respiratory protection against harmful airborne substances.
How to Avoid:
Establish a Program: Develop a respiratory protection program that includes fit testing and medical evaluations.
Training Sessions: Conduct training sessions on the proper use and maintenance of respirators.
Hazard Assessments: Regularly assess the workplace for respiratory hazards and update protection measures accordingly.
5. Lockout/Tagout
Lockout/tagout procedures prevent accidental machine start-up during maintenance or servicing, with 2,443 violations reported in 2024.
How to Avoid:
Written Procedures: Create clear lockout/tagout procedures that comply with OSHA standards.
Employee Training: Train employees on these procedures and ensure they understand their importance.
Regular Audits: Conduct regular audits of lockout/tagout practices to ensure compliance.
6. Powered Industrial Trucks
This standard covers forklifts and other powered industrial trucks. In 2024, 2,248 citations were issued due to improper operation or lack of training.
How to Avoid:
Operator Training Programs: Implement comprehensive training programs for all forklift operators.
Inspection Protocols: Establish daily inspection protocols for powered industrial trucks before use.
Safety Procedures Enforcement: Enforce strict adherence to safety operating procedures while using powered industrial trucks.
7. Fall Protection – Training Requirements
With 2,050 citations in 2024, this violation emphasizes the need for proper training regarding fall protection systems.
How to Avoid:
Regular Training Sessions: Conduct regular training sessions focused specifically on fall protection.
Documentation of Training Completion: Keep detailed records of employee training sessions as proof of compliance.
On-the-job Training Opportunities: Provide opportunities for hands-on training in fall protection equipment usage.
8. Scaffolding
Scaffolding violations totaled 1,873 in 2024, often due to improper assembly or lack of safety measures.
How to Avoid:
Follow Manufacturer Guidelines: Ensure scaffolding is erected according to manufacturer specifications.
Frequent Inspections: Conduct frequent inspections of scaffolding structures before use.
Employee Training on Scaffolding Safety: Provide training on safe scaffolding practices and potential hazards.
9. Personal Protective Equipment – Eye and Face Protection
Eye and face protection violations were cited 1,814 times in 2024 due to inadequate provision or enforcement of PPE usage.
How to Avoid:
Assess Workplace Hazards: Regularly assess the workplace for potential eye and face hazards.
Provide Appropriate PPEs: Ensure that appropriate eye and face protections are available for all employees exposed to risks.
Enforce Usage Policies: Develop policies that enforce consistent use of PPE when required.
10. Machine Guarding
Machine guarding violations accounted for 1,541 citations in 2024, highlighting the need for effective safeguards against machine-related injuries.
How to Avoid:
Install Proper Guards: Ensure all machines have appropriate guards installed as per OSHA standards.
Conduct Regular Inspections: Regularly inspect machinery for proper guarding and functionality.
Employee Training on Machine Safety: Train employees on the importance of machine guarding and safe operating procedures.
Conclusion
Understanding these top OSHA safety violations is crucial for fostering a safe work environment. The most frequently cited examples of OSHA violations include fall protection requirements, hazard communication standards, ladder safety protocols, respiratory protections, lockout/tagout procedures, powered industrial truck operations, fall protection training requirements, scaffolding safety measures, personal protective equipment usage, and machine guarding standards.
To avoid these violations:
Implement comprehensive training programs tailored to each specific hazard.
Conduct regular inspections and audits to ensure compliance with safety standards.
Establish clear written procedures
that all employees can easily understand and follow.
Create a culture of safety where employees feel empowered to report unsafe conditions without fear of retaliation.
Employers can significantly reduce the risk of accidents by prioritizing workplace safety through proactive measures and continuous education about examples of OSHA violations while enhancing overall productivity and morale within their organizations. This commitment not only protects employees but also contributes positively to business performance in today's competitive landscape.